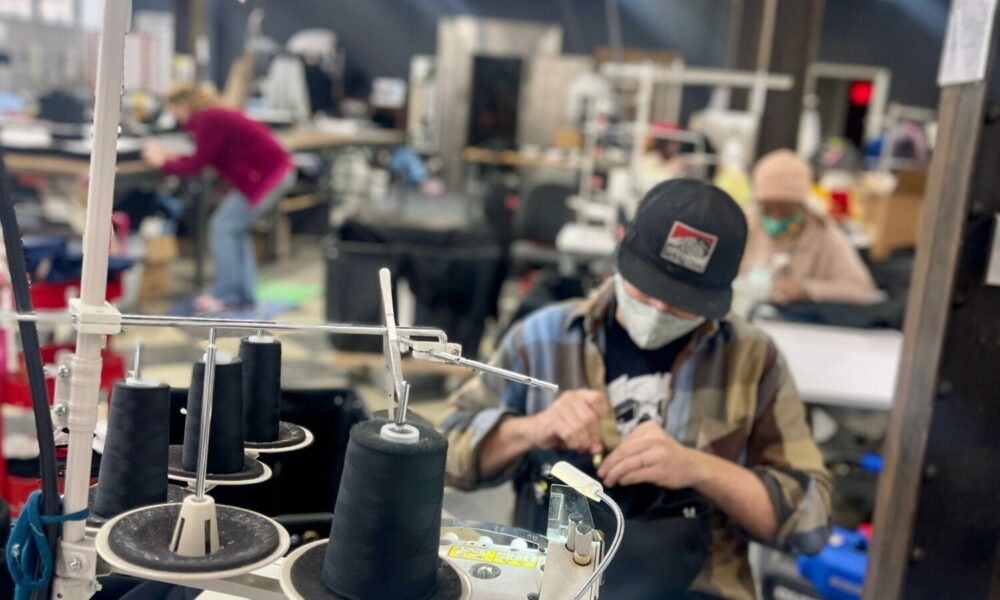
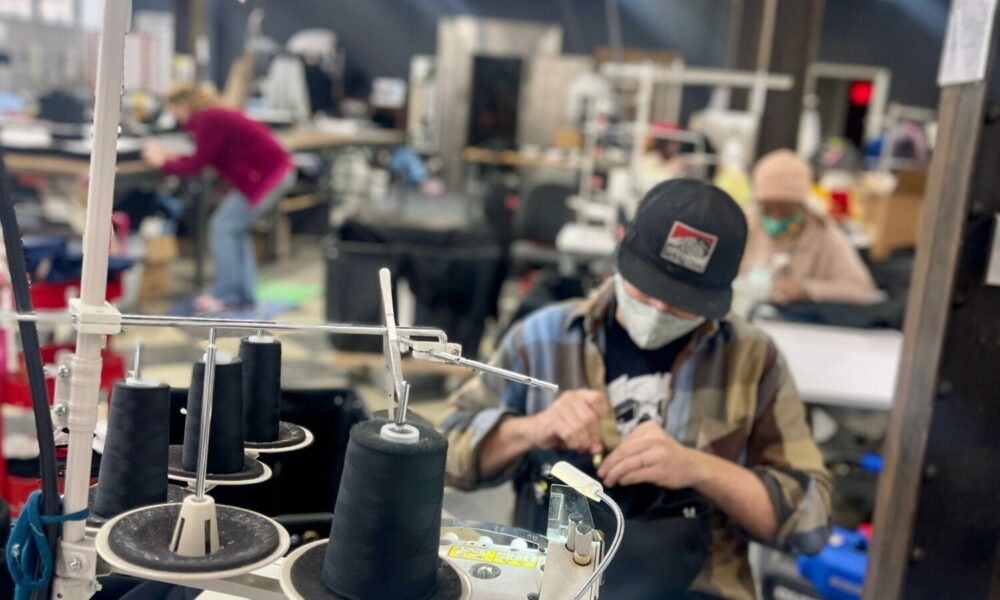
Today we’d like to introduce you to Karen Buscemi.
Hi Karen, thanks for sharing your story with us. To start, maybe you can tell our readers some of your backstories.
Detroit Sewn opened its doors in Pontiac in 2015 in response to the need for full-service cut and sew in Michigan. Our journey began with one sewer, one client, and one project. Since then, we have expanded four times and serviced hundreds of clients from all over the country, who all value making in the U.S.A.
As a result of the COVID-19 pandemic, in March 2020, Detroit Sewn pivoted to manufacturing PPE. We partnered with two auto suppliers and a couple of smaller factories in the area to help us produce face masks and isolation gowns for hospitals, hospital supply companies, nonprofits, and counties. During that time, we collectively produced more than 500,000 face masks and 75,000 isolation gowns.
The pandemic pointed out the blatant need for a stronger U.S. supply chain, and after a year and a half of producing sustainable PPE for hospitals around the country, we decided to next take on the blanks industry (clothing and accessories that are purchased “blank” and then decorated with logos or art) to be a go-to U.S.-manufactured option.
“When I opened the factory, my original goal was to manufacture apparel for beloved local brands that were decorating and selling them,” says Karen Buscemi, President & CEO of Detroit Sewn. “Now is the right time to go down this road – with a special emphasis on branding corporate gear – thanks to the name and reputation we’ve built over the years paired with the supply chain issues causing huge inventory shortfalls for U.S. companies large and small.”
With multiple high-quality basics currently available, ranging from t-shirts to hoodies, we will continuously be adding to our product list.
In addition to manufacturing the apparel and accessories, we decorate them, too, utilizing a wide variety of high-end heat transfer options.
A socially responsible manufacturer, our retail sales are made to order to combat the wastefulness found globally in apparel manufacturing. Orders are cut, sewn, and shipped within two weeks.
We all face challenges, but looking back would you describe it as a relatively smooth road?
You can’t own a sewing factory and expect anything to be smooth. Something goes wrong every single day, whether it’s a supply chain issue or trying to bring a complex product idea to life and make it production-friendly.
Our greatest strength is our flexibility. We continuously face challenges in this industry. We have to be open-minded and never say, ‘That’s all we can do.” There is always something else we can do. We are a team of creatives, so we continuously push for creative problem-solving. And we never think that the only solution is our solution. We were able to successfully pivot the factory to PPE because of flexibility both in mindset and in the team’s abilities.
Appreciate you sharing that. What should we know about Detroit Sewn, Inc?
Notable Facts
-Detroit Sewn President & CEO Karen Buscemi has had a fashion nonprofit, Detroit Garment Group, since 2012 that focuses on business education and economic development. It was because of all the inquiries her group received for manufacturing opportunities in the area – and the lack of resources that she found – that she launched Detroit Sewn, Inc. in August 2015.
-We are both WOSB and HUBZone certified.
-The first four years of our business were spent responding to the need for full-service cut and sew in Michigan. During that time, we helped launch dozens of brands that we took from idea to full production that they were then able to sell to their customers – all made in the USA.
-In 2020, we pivoted to manufacturing PPE, and along with multiple partners, including two automotive suppliers, Detroit Sewn led the charge in keeping a large hospital system – with hospitals in 22 states – up and running with more than 500,000 reusable masks and 75,000 reusable isolation gowns.
-For eight weeks during the early months of the PPE crisis, Detroit Sewn created the Michigan Mask Donation Center, got its landlord to donate the space next door to the factory to hold the temporary Center, enlisted the help of Glamorous Moms Foundation to run it, and used all its media contacts to raise awareness. Thanks to the generous donations of pre-washed sewn masks from our local home sewers, we had enough inventory to give 7,050 masks to 390 community groups, families, individuals, businesses, and non-profit organizations in Southeast Michigan.
Services
Pre-Production: Product development, pattern making, sample making, size grading, materials sourcing, tech packs
Production: Fabric cutting, contract sewing, label/patch sewing, dye sublimation, heat transfers, oops manufacturing
What matters most to you? Why?
Every day at the factory, what matters most to us includes:
-Having a factory that doesn’t feel like a factory. We are in a corner building lined with windows and beautiful natural light. We have a cozy employee lounge area, and no offices so we are all together.
-Truly working as a team, problem-solving as a whole group, and letting everyone be as creative and experience as much growth as they can.
-Creating a quality, detail-oriented and friendly experience for our clients that ensures they will come back to us time and time again. We still work with many customers that we started with five and six years ago. We are happy this is where they want their products made.
-Producing our own products that are manufactured in Michigan. This is a big one.
Contact Info:
- Email: [email protected]
- Website: detroitsewn.com
- Instagram: Instagram.com/detroitsewn
- Facebook: Facebook.com/detroitsewn
- Twitter: Twitter.com/detroitsewn